
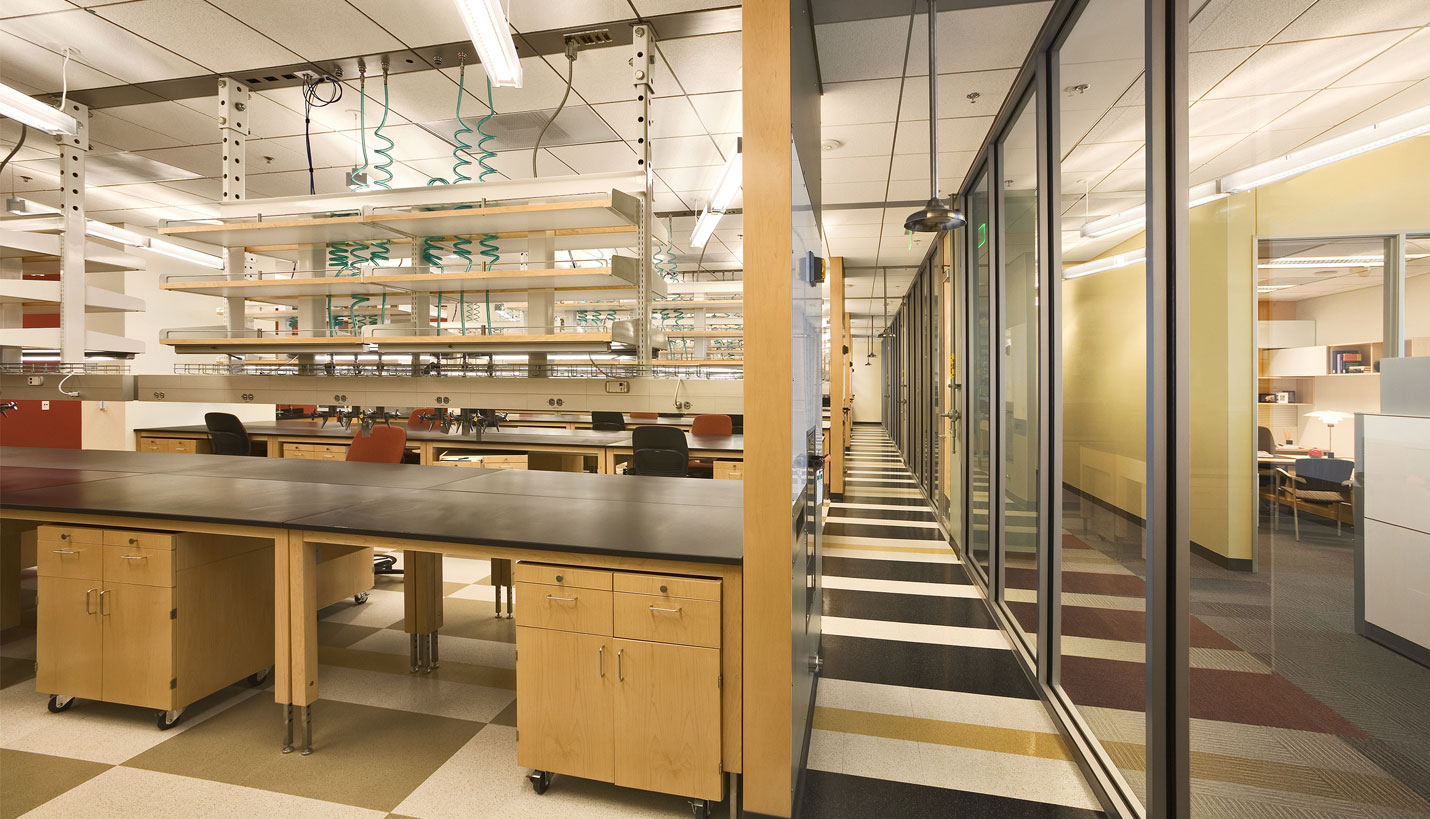
Collaborate to Design, Build a Lab: Three Essential Tactics
Page Senior Principal Michael J. Mace explains how to properly execute laboratory design/builds.
Design/build can fast-track laboratory projects—or it can confuse issues and slow projects to a crawl. Getting design/build right requires three collaborative strategies to guide architects builders, and owners through a project:
- First, all three stakeholders must make a conscious commitment to collaboration.
- Second, the parties must complete a collaborative pre-design analysis. This process is designed to fix problems before they work their way into the bricks and mortar—and become more expensive to fix.
- Finally, the architect and contractor must work together to develop a flexible design scheme that facilitates changes during construction.
Whether reactive or proactive, these three strategies come into play on every design/build job. Reactive collaboration is also known as troubleshooting. Should a problem arise halfway through the masonry work, for example, the owner, architect and contractor will have to meet, define the problem and figure out how to fix it. This will slow the project and raise its cost.
These collaborative strategies are particularly important to design/build laboratory projects. Labs are complex buildings, which often employ sophisticated technologies that require exacting environmental control and/or regular upgrades.
Commitment to collaboration
By committing to collaboration on a job, the owner, architect and contractor acknowledge that problems will arise that threaten the project’s schedule and budget. Such problems tend to revolve around design elements that the owner doesn’t like, the contractor finds too expensive to purchase or construct, the architect wants to retool—or that simply don’t work.
On collaborative projects, the parties find and work out these issues. The effort starts with the pre-design analysis and continues through the project’s final commissioning.
The process begins as the designer develops an understanding of the owner’s needs and conceptual options. Then, all parties discuss which options appear to satisfy the owner’s requirements, while allowing some flexibility to move in other directions if necessary.
The goal of collaboration at this stage is to discover, raise and settle as many big-picture issues as possible as early as possible, before they affect the budget or schedule. The idea of commitment to collaboration resembles strategic planning, except that it is designed to lay out strategies for a single project and its design/build delivery method. As always, if the strategy is right, the execution will follow more smoothly.
Pre-design analysis
The objective of the pre-design phase is to develop a complete and thorough understanding of the performance requirements to be met by the design solution.
To this end, the design team must establish a true rapport with both the client (owner) and with the future facility users (or their surrogates) very early on. Interaction (on-location) with the client’s team is essential and should involve a number of people from the both client team and the design team. The interaction should be structured and logically sequential—going from the general (client vision and major goals) to very specific and detailed (individual room requirements).
The interactive programming process is actually simultaneous qualitative and quantitative analysis that not only systematically identifies the facility requirements but also helps build consensus and a shared vision among the participants. The process relies on on-location interviews and work sessions to collect information, identify issues/problems, solicit ideas, construct consensus and develop requirements (including detailed workflow and adjacency needs).
Five steps are used for seeking both quantitative and qualitative information:
- Establish goals.
- Collect, organize and analyze facts (e.g., staff counts, site analysis).
- Uncover and test concepts (ideas to implement the goals).
- Determine needs (space list, cost estimate, time requirements).
- State the (architectural performance) problem (the essence and uniqueness of the project).
Each of these steps is influenced by four characteristics: function, form, economy and time, which are applied to the steps in the process of discovering the comprehensive nature of the entire design problem. The steps help to create an information framework for organizing, communicating, evaluating and making decisions on the project.
This covers questions as to the type of lab—college or university, pharmaceutical research, government research, or some other kind of facility—type of research to be done, the number of people who will work there, site characteristics, and floorplan.
In addition, the team should know what kinds of research activities can be accommodated, what kinds of technology the facility will provide for researchers, which building systems will require sustainable design elements, and proposed budget and schedule.
Answering these questions often requires the team to expand its collaborations to include end users. In pharmaceutical research facility design, for instance, interviews with scientists, executives and administrative staff can help establish workflow requirements and elicit critiques of problems encountered in existing facilities. Interviews often turn up issues that might be easy to overlook in light of the focus on workflow.
For another example, a university chemistry lab will likely offer easy access to students, faculty and visitors throughout the day. Thus after-hours security may be necessary, in the form of access control technology and/or extra attention from campus patrols. How might the building design accommodate these needs?
A pharmaceutical lab will also require security systems capable of protecting intellectual property stored electronically and on paper.
As the analysis moves from big-picture concepts to concrete details, the design team and contractor must challenge the owner’s concept components that will lengthen schedule and increase budget. In cases where the owner stands firm, the team must agree to find extra time or dollars in other agreed-upon areas of design.
The owner and project team identify cost elements of the project such as exterior façade construction, structural framing options, mechanical systems, electrical systems and other categories to quantify the budget dollars for the project. This allows the whole team to work together to determine fiscal priorities. For instance the architect may consider a more economical exterior skin design to reduce cost in that category so that additional dollars could be moved to the mechanical systems budget to provide a more robust exhaust system.
Little more than concepts have been committed to paper by this point, while conceptual schematics continue to be developed. By and large, however, the commitment stage and the pre-design analysis help the team get to know each other’s requirements and define the project.
Flexible design scheme
By the time the team arrives at the point where they put the third strategy into play, then, they understand each other’s requirements and the project well enough to know how to build flexibility into the design scheme.
This is an important capability considering that a laboratory is not as flexible as, for instance, an office building, whose infrastructure stays the nearly the same regardless of tenant, while interior elements are easily changed out.
Labs, conversely, house both scientists with extraordinary infrastructure needs and administrators with general business office needs. Scientists may need large data communications capabilities to transmit complex images. They may further need specialized HVAC systems to maintain recirculated filtered positive air pressure to keep dust out of a clean room, or negative pressure in a chemical lab to keep the fumes away from the occupants in the lab. A computer lab may combine unusual power needs with data transmission capabilities.
In addition, laboratories today may combine elements of computer laboratories with those of chemistry laboratories, as computers are needed to evaluate the experimental results. After a time, the chemistry lab might be converted to a medical diagnostics lab.
For all of these reasons, laboratories require flexible design schemes with the ability both to ramp up power for one application, and to deliver consistently high data transmission speeds for another application.
However, a flexible design plan that satisfies the many diverse requirements of a modern laboratory could be difficult to create using a conventional design/bid/build or construction management delivery method on a project with a tight schedule.
To achieve “speed to market,” many lab projects use the design/build delivery method because they are on fast-track schedules—which provide less time to conceive and implement effective flexible design solutions.
Hence it is important to aim for flexibility in a design/build laboratory project from the beginning. The usual approaches apply. Widely spaced columns and spacious horizontal areas allow users to configure and reconfigure space without bumping into barriers.
In laboratories, the longer column spans must still provide plenty of support for large floor and ceiling crawl spaces, which will hold more than the normal quota of HVAC, electrical and network-related infrastructure.
Finally, and perhaps paradoxically, design flexibility must not complicate the flow of work from design through approval to construction. In a design/build project, the design team typically delivers drawings for the next phase of construction work “just in time” as the contractor is ready to begin that phase.
Such a tight schedule, occurring during the frenetic pace that design/build projects so often keep, can tempt project members to sign off on concepts and drawings without carefully evaluating them.
In the end, collaboration, creativity and decision evaluation are the keys to a successful project. Maintain the collaboration of the project team between the owner, architect and contractor, with the understanding that getting as much right as possible the first time, will preserve both the project budget and schedule—and make for a more successful facility.
02/23/2015
People
Related Posts
- Collaboration: Key to successful project delivery
- Responding To A Community Challenge
- Case Study: Award-winning Non-profit Healthcare Clinic
- Elevating Austin through art + architecture
- Industry Collaboration For Greater Good
- Design That Makes A Difference: Healthcare for the Homeless
- Providing Health, Hope & Dignity