
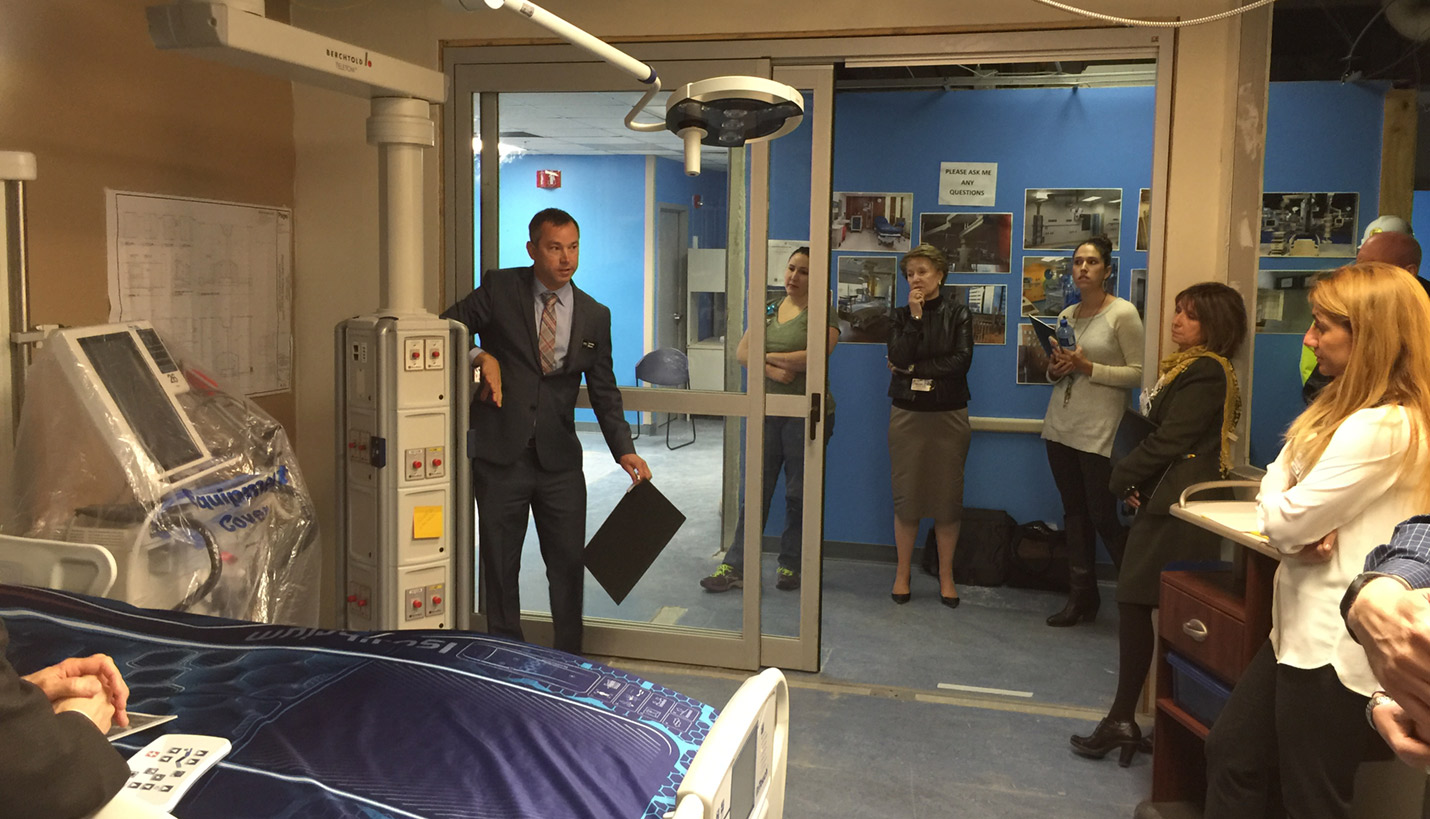
Case Study: A Typical Medical / Surgical Patient Room Design Mock-up
The project’s original design was based on a 30’x30’ structural bay with two patient rooms centered within each bay. As the design progressed, it became clear the project budget could not accommodate the building that would result. The project team was determined to do everything possible to retain the same number of key-driver spaces in the project yet reduce the overall square footage of the building by over 15%. Along with other space reduction strategies, the structural bays were reduced to 28’. Since the priority remained with centering two rooms per bay, this change would substantially impact the size of the patient room. The design team knew that in order to ensure our client would get the best design we would have to take that room to a full-sized mock-up to help us accurately portray the design and elicit quality input from clinical staff.
For the patient room, one of the ideas we developed was the concept of co-locating all of the miscellaneous room attributes associated with the clinical provider into one location. These attributes included the hand washing sink, soap dispenser, towel dispenser, sharps container, glove dispenser and white board. These items are always different sizes, multi-colored and generally are not that attractive to look at. They commonly convert the feel of a well-designed room that previously looked like a hotel room into, yes, a hospital room - not exactly what we wanted in this particular facility.
Once we decided to pursue the mockup we contacted the project equipment planner and asked them to help us get actual items that would be specified for the room; patient bed, over bed table, sharps container, glove dispenser. We went to a local restaurant supply house and purchased inexpensive towel and soap dispensers. We contacted a plumbing supply representative and asked him to bring us a gooseneck sink faucet and hand washing sink. We ordered foam core, hot glue strips, PVC piping to simulate handrails and a lot of tape. We assigned a project designer to spearhead the effort, recruited a couple of our summer interns and went to work.
In just a week, foam-core room walls were up, major architectural room features were built and preliminary placements of room attributes were installed per the design at the time. Once we stepped back from it all, we realized what a true benefit the mock-up process was because if we had built 70 of these rooms as designed on the documents, we would have had a big mistake in the field. The design had previously been vetted by senior healthcare planners, equipment planners, interior designers, and most importantly the clinical staff but when the full-scale mock-up was built, we realized numerous changes would be required. In this situation, they were not significant elements like location of walls but countless small revisions to all of the items that were to be placed in the room, sometimes just relocating them by inches.
04/19/2017
Related Posts
- Room Mock-ups & Their Utilization In The Design Process
- Best in Brick: Baylor Surgical Hospital at Fort Worth
- Fort Worth Park Place Celebrates New Baylor Surgical Hospital
- New Hospital Brings "Next Generation" Healthcare to the Houston Bay Area
- Construction Begins on New Medical Center in Austin
- $135M hospital breaks ground in Williamson County